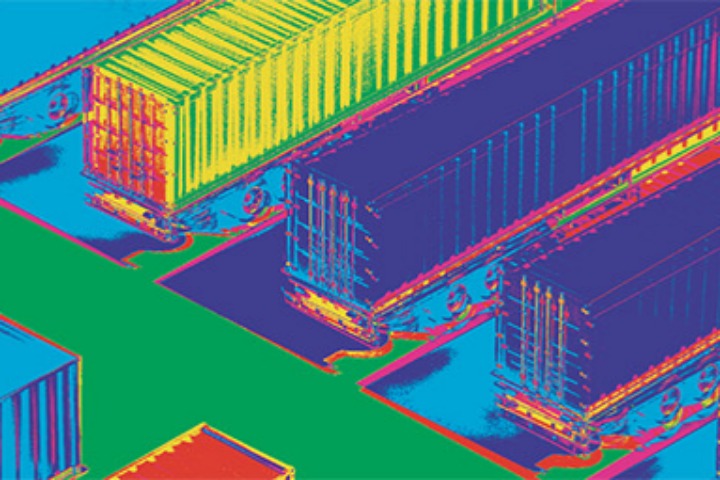
Yard Management Systems Update: From “black holes” to high visibility
With capacity crunches, driver shortages and new government regulations all pushing companies to transform themselves into “shippers of choice” for their carriers and logistics providers, more of those shippers are starting to see their yards as valuable assets versus just storage grounds.
After all, the yard is literally the first thing that a driver sees when he or she comes onto the premises; the area where vehicle movement has to be carefully orchestrated for maximum efficiency; and the last place of interaction for a driver on the way out the door.
For many, turning the yard into an active, valued link in the supply chain means completely rethinking the way that area of the warehouse or distribution center (DC) has been managed for decades. That’s because companies haven’t spent much time improving yard processes or investing in yard technologies, and instead put the most effort into optimizing yard assets, cutting driver detention time and adjusting priorities according to receiving and shipping volumes.
“Poor yard visibility and management are pretty common issues,” says Bart De Muynck, Gartner’s research vice president, transportation technology. Technology can help fill those visibility gaps and help the yard become more than just a “black hole,” he continues, but simple trailer identification solutions don’t always do a complete job. “It’s not always that companies don’t know what’s out there, they probably have a general sense of it,” says De Muynck. “They just don’t know where those assets are.”
Enter yard management systems (YMS), one of the least-used solutions in the supply chain software lineup. According to Logistics Management’s most recent Technology Usage Study, only 8% of companies are currently using YMS. Ranging from systems that note manual entries of asset movements entering and exiting the yard, as well as movements in and out of parking spaces, YMS also includes more advanced platforms that incorporate real-time, asset-tracking technologies, such as trailer telematics, RFID and related technologies, Gartner reports in its latest “Market Guide for Yard Management.”
Filling in the gaps
In its simplest form, YMS automates the tracking of assets (e.g., trailers or containers) in a yard. In doing so, the software facilitates the process of efficiently locating, handling, and moving those assets. In turn, the software helps to increase the visibility of gate operations, yard processes and dock-door activities.
According to Gartner, YMS also includes a set of capabilities that deals with the management and process execution activities related to or affecting a company’s shipping yard and dock doors—factoring in equipment, facility and employee constraints as well as activity demand.
Often implemented as part of the extended capabilities of a warehouse management system (WMS), YMS can also be part of a transportation management system’s (TMS) extended offering. Advanced YMS capabilities are also offered as a standalone solution by vendors like PINC. Shippers using the software typically rely on it to help close the supply chain gaps that exist in their own backyards.
“Some of these gaps consist of long trailer wait times,” De Muynck notes, “unproductive personnel numbers, poorly synchronized movement of goods, and ineffective dock planning.”
Not a whole lot of buzz
Shippers may be looking more closely at how to make their yards more efficient, but that hasn’t necessarily raised awareness of the need for YMS.
“There’s some interest there, but not a whole lot of buzz,” says Clint Reiser, research analyst at ARC Advisory Group. “That explains how vendors like PINC have their own niches in this sector, and how companies like SAP can charge an additional fee for managing really complex yards.”
Noting that SAP has an advanced YMS that’s sold separately from its extended warehouse management (EWM) solution, Reiser says that option is usually best suited for very complex yard setups (i.e., container yards), “where the yard is the cornerstone of the shipper’s whole operation.”
Joe Vernon, Capgemini’s practice leader of supply chain analytics, says that he’s starting to see “a bit of an increased interest in yard management,” with more companies looking at metrics like dwell time, detention time, average wait time and other factors that can impact their total logistics costs.
“Because the companies now have that data at their avail, they’re picking up on alarming trends—like how carriers are experiencing five- or six-hour average wait times at certain facilities,” Vernon explains. “Having trucks backed up like that—waiting to be loaded or unloaded—can lead to some major inefficiencies out in the yard.”
Shippers that ignore the need for good yard management do so at their own peril. According to Vernon, even just a few vehicle backups out in the yard can also hit a shipper’s bottom line. Carriers are charging detention fees, customers want their orders quickly, and drivers’ behind-the-wheel hours are limited by the hours of service (HOS) rule and more closely monitored thanks to the new electronic logging device (ELD) ruling.
Carriers are also being more selective about the shippers that they work with because, well, they can afford to be in today’s freight environment. “Carriers make money when their trucks are on the road,” says Vernon, “not when they’re sitting around waiting.” Knowing this, Vernon says more companies are looking at implementing solutions that range from simple tools that help with yard scheduling and appointments to full-blown YMS.
“The yard is still a black hole, but at least shippers now know where that black hole is and they have some data points that can help them start pushing the envelope and do something about it,” Vernon says. “The yard is an area that prevents shippers from truly collaborating with carriers, many of which are refusing to accept tender from shippers with yard inefficiencies.”
For Cummins, YMS is a game-changer
As a manufacturer of power solutions, Cummins, Inc., makes everything from diesel and natural gas engines to hybrid and electric platforms. It also makes the related technologies, including transmissions, battery systems, fuel systems, controls, air handling, filtration, emission solutions, and power generation systems. Headquartered in Columbus, Ind., the global company was using a YMS that included a map of its yard that enabled the manual movement of trailers and the checking in and out of those assets.
Every piece of information had to be entered manually, according to Rebecca Koch, transportation manager for the company’s Memphis DC, which meant that the yard manager had to perform a yard check a few times a day, update the system, and then provide a yard snapshot at that point in time to different teams. “Since the snapshot would be outdated almost instantly,” Koch says, “the different operations teams had to perform yard checks as well.”
As part of that yard management approach, drivers were given devices that enabled direct communication with the transportation team. “When a driver received a move request, the first step was to locate the trailer,” Koch says. “Because there was no real-time tool, at times the driver had to go around and search for it. Once located, the asset had to be moved in a specific door, but the door may have already been occupied.”
In those scenarios, the driver would either have to call back and request a different door or find one and then let the team know where the trailer had moved. During peak times, drivers would have to remember multiple moves and the order in which to move them. “When there were multiple drivers during peak times, the workload among drivers was unevenly balanced,” says Koch. “This setup lead to confusion and a lot of unnecessary phone calls, and ultimately slowed down operations.”
https://www.logisticsmgmt.com/article/yard_management_systems_update_from_black_holes_to_high_visibility/technology
Comments